pRODUCTION CONTROL
~The average delivery delay per year: Achieved zero defects by strict control procedure ~
1, Controlling production progress by ERP system and computers
* Adopting ERP system to manage automatically orders, quantity, shipping date by computers.
- Prompty finding and handling late delivery problems arising out through each process.
- Preventing product defects arising from manual operations and miscommunication.
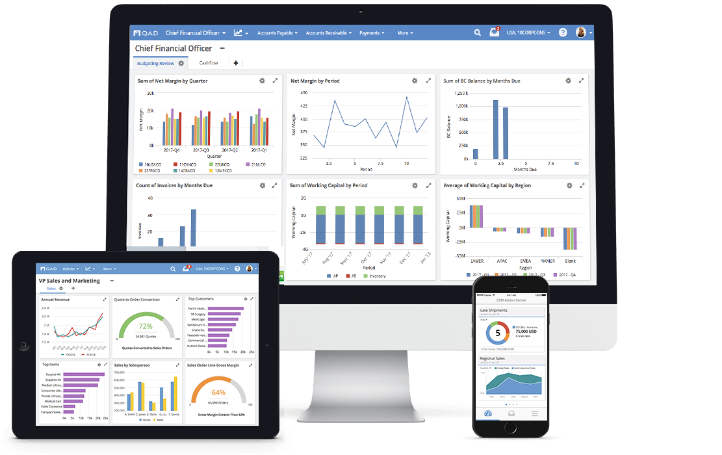
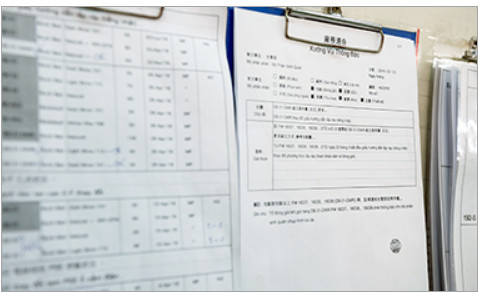
2, Enhancing the acceptance and understanding among employees about notification matters
Any changes on specifications, quantities, other change requests shall be shown on the signboard as specified by each departments to notify everybody.
- All employees can understand clearly when the new requirements were given to them to avoid miscommunication.
3, The semi-automation due to the introduction of roller conveyor system and the development of our original machines.
* Helping facilitate the smooth transportation by using the roller conveyor system instead of pallet jack.
- Preventing product damage as well as reducing the time loss.
* Through joint development with equipment manufacturers to introduce the genuine equipment for multi-stage operation simultaneously.
- Reducing of mass production cost as well as improvement of the product accuracy.
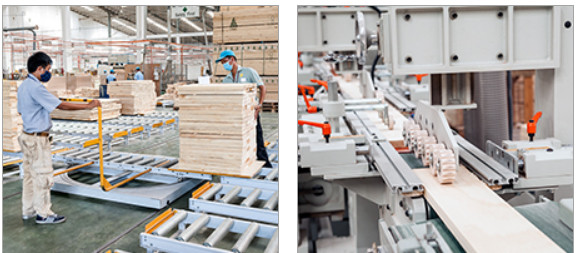
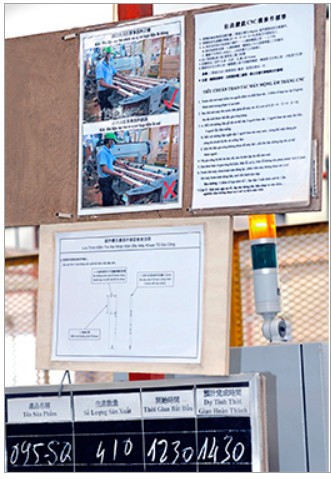
4, Safety measures for employees using of machines.
* Representing all operation methods, using precautions on the board and visualizing such notifications for all machines.
- All employees can operate the equipment after clearly understanding the method.
* Furthermore, the content of operations, starting time – ending time, check points are also shown and visualized on the board for each machines.
- Employees can operate explicitly and consistently.
5, General Production Meetings every morning and Individual Department Meetings held once a week
* General Production Meetings every morning
- The departments prompty raise, review and resolve the problems arising every day.
* Individual Department Meetings held once a week
- Implementing the investigation of the causes, consideration of improvement of problems incurred in previous week.
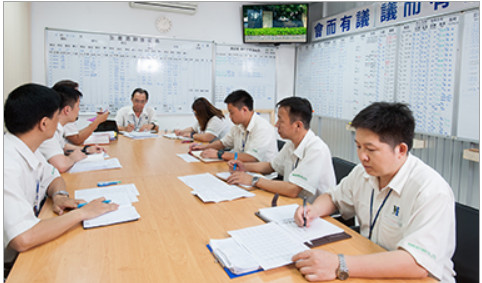